Quality Assurance
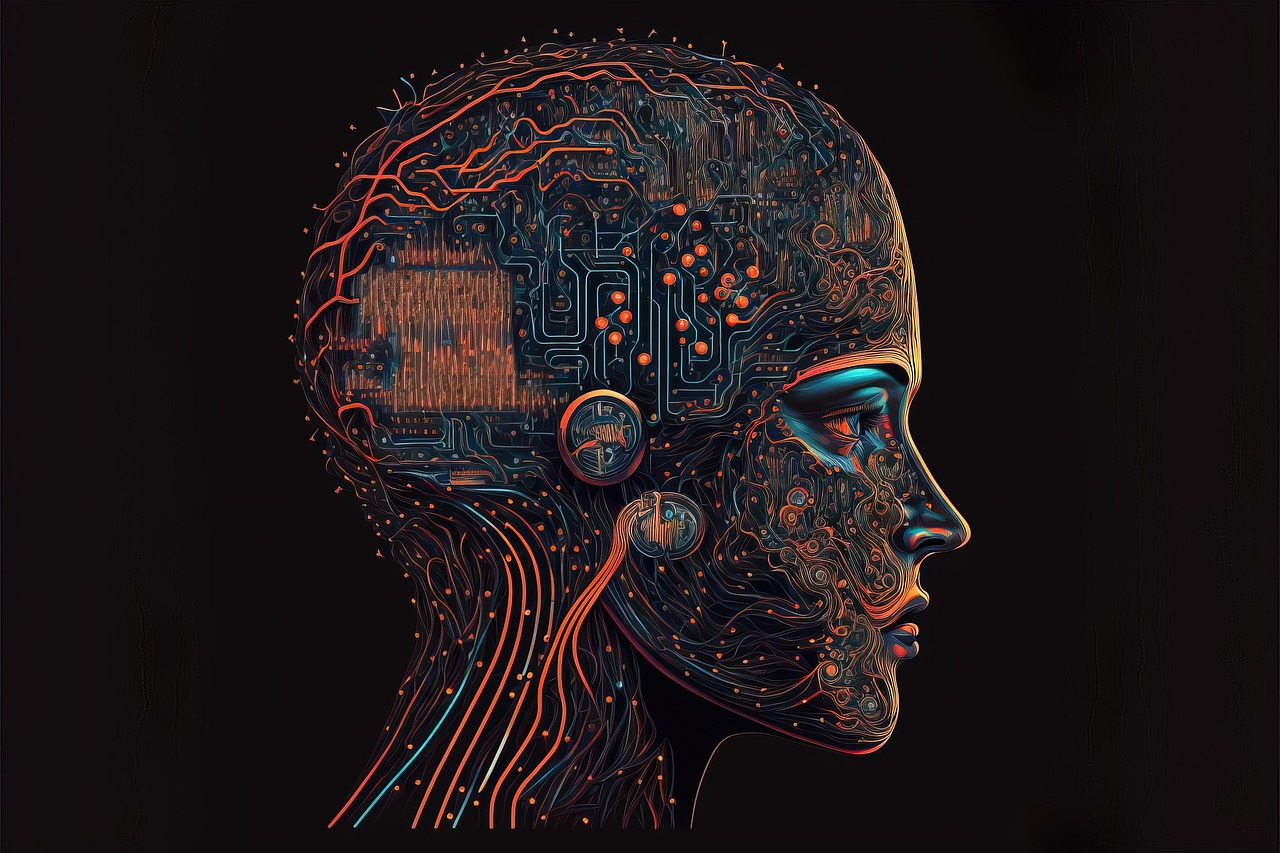
Ensuring Excellence: The Role of Quality Assurance in Manufacturing
Introduction
Quality assurance is a cornerstone of success in the manufacturing industry, where delivering high-quality products is essential to maintaining customer satisfaction and brand reputation. As manufacturers face increasing pressure to meet stringent quality standards, quality assurance has become a strategic priority. At Chamco Digital, we’re helping manufacturers achieve quality assurance through our expertise in cloud technology, AI, and Microsoft Azure, ensuring they can deliver products that meet the highest standards.
The manufacturing industry operates in a competitive landscape where quality issues can lead to costly recalls, customer dissatisfaction, and regulatory penalties. A 2024 report by Deloitte found that quality defects cost manufacturers $500 billion annually, highlighting the need for robust quality assurance processes. Quality assurance uses technology to monitor, analyze, and improve production processes, ensuring that products meet specifications and customer expectations.
In this blog post, we’ll explore how quality assurance is transforming the manufacturing industry, the benefits it offers, and the challenges of implementing these solutions. We’ll also discuss how Chamco Digital, through our partnership with Microsoft Azure and expertise in cloud migration, is helping manufacturers implement quality assurance systems that drive excellence. Join us as we dive into the future of manufacturing, where quality assurance ensures product excellence and customer satisfaction.
The Need for Quality Assurance in Manufacturing
The manufacturing industry relies on consistent quality to maintain customer trust and comply with regulations. However, several challenges make quality assurance a critical priority:
- Quality Defects: Defects in products can lead to recalls, returns, and reputational damage, impacting profitability and customer loyalty.
- Regulatory Compliance: Manufacturers must comply with strict standards, such as ISO 9001, to ensure product safety and quality, with non-compliance leading to fines and legal issues.
- Customer Expectations: Consumers demand high-quality products, and even minor defects can lead to dissatisfaction and loss of business.
- Complex Production Processes: Modern manufacturing involves complex processes with multiple variables, making it difficult to maintain consistent quality.
- Cost of Rework: Identifying and fixing defects after production is costly and time-consuming, increasing operational expenses.
Quality assurance addresses these challenges by using technology to monitor production processes, detect defects in real time, and ensure compliance with standards. By adopting quality assurance systems, manufacturers can reduce defects, lower costs, and enhance customer satisfaction, ensuring they remain competitive in a global market. At Chamco Digital, we believe that technology is the key to unlocking these benefits, enabling manufacturers to build quality assurance systems that deliver excellence.
How Technology Enables Quality Assurance
Technology is transforming quality assurance by providing tools to monitor, analyze, and improve production processes. Here’s how key technologies are making a difference:
- AI and Machine Learning: AI can analyze production data to detect defects, such as identifying anomalies in product dimensions or materials. For example, AI can flag a defective part on an assembly line before it reaches the final product. Chamco Digital leverages Microsoft Azure’s AI capabilities to help manufacturers implement these quality assurance solutions, ensuring high accuracy.
- IoT and Real-Time Monitoring: IoT sensors on production equipment collect real-time data on quality metrics, such as temperature, pressure, or surface finish, enabling manufacturers to detect issues immediately. For instance, a sensor can detect a deviation in a product’s weight, triggering an alert. Chamco Digital integrates IoT with Azure, ensuring that manufacturers can monitor quality in real time.
- Cloud-Based Quality Management: Cloud platforms like Microsoft Azure provide a centralized system for managing quality data, enabling real-time analysis and reporting. Azure’s analytics tools can track quality metrics and identify trends, such as recurring defects. Chamco Digital’s cloud solutions streamline quality management, ensuring that manufacturers can maintain high standards across their operations.
- Computer Vision: Computer vision systems use cameras and AI to inspect products for defects, such as scratches or misalignments, with greater accuracy than human inspectors. For example, computer vision can detect a crack in a metal component during production. Chamco Digital’s expertise in computer vision ensures that manufacturers can implement automated inspection systems that enhance quality.
- Data Analytics and Visualization: Data analytics provide insights into quality performance, while visualization tools like Microsoft Power BI offer dashboards to monitor metrics. For instance, a dashboard can show the defect rate for a production line, enabling managers to take action. Chamco Digital’s expertise in data analytics ensures that quality insights are actionable and accessible.
These technologies work together to create a quality assurance ecosystem that reduces defects, ensures compliance, and improves product quality in the manufacturing industry.
Benefits of Quality Assurance
Achieving quality assurance offers numerous benefits for manufacturers:
- Reduced Defects: Real-time monitoring and AI-driven analysis reduce defects, ensuring that products meet specifications. A 2024 study by PwC found that quality assurance systems reduced defect rates by 30%.
- Cost Savings: By detecting defects early, quality assurance lowers the cost of rework, recalls, and returns, saving manufacturers millions annually.
- Regulatory Compliance: Quality assurance ensures that products meet industry standards, such as ISO 9001, avoiding fines and legal penalties.
- Improved Customer Satisfaction: High-quality products enhance customer satisfaction, leading to increased loyalty and repeat business.
- Competitive Advantage: Manufacturers with robust quality assurance systems can differentiate themselves in the market, attracting new customers and retaining existing ones.
Chamco Digital enhances these benefits by providing end-to-end cloud solutions that integrate seamlessly with existing systems. Our partnership with Microsoft Azure ensures that manufacturers can leverage the latest quality assurance tools, while our managed IT services provide ongoing support to maintain performance and compliance.
Challenges in Quality Assurance
While the benefits are clear, achieving quality assurance comes with challenges:
- Data Quality: Quality assurance relies on accurate data, but many manufacturers struggle with incomplete or inconsistent datasets. Chamco Digital helps manufacturers implement data governance frameworks, ensuring that data is reliable.
- Cost of Implementation: Implementing quality assurance technologies can be costly, particularly for smaller manufacturers. Chamco Digital offers cost-effective cloud solutions that scale with a manufacturer’s needs, making quality assurance accessible to all.
- Integration Complexity: Integrating quality assurance systems with existing production processes, such as MES or ERP systems, can be complex. Chamco Digital’s cloud migration services ensure seamless integration, enabling manufacturers to implement quality assurance without disruptions.
- Skills Gap: Quality assurance requires specialized skills, such as AI and computer vision expertise, which many manufacturers lack. Chamco Digital’s team of experts bridges this gap, providing the expertise needed to implement and maintain quality assurance solutions.
- Change Management: Implementing quality assurance often requires changes to workflows and roles, which can lead to employee resistance. Chamco Digital supports change management by providing training and support, ensuring a smooth transition.
Addressing these challenges requires a strategic approach that combines technology, expertise, and a commitment to quality. Chamco Digital is well-equipped to help manufacturers overcome these hurdles and achieve quality assurance.
Real-World Applications and Case Studies
Quality assurance is already making a significant impact in the manufacturing industry. For example, a 2024 McKinsey report highlighted how a major electronics manufacturer used AI and computer vision to reduce defect rates by 25%, saving $2 million annually in rework costs.
Another example is a food and beverage manufacturer in the UK, which used IoT to monitor quality during production, as noted in a 2025 industry report. The company reduced quality-related returns by 15% and improved customer satisfaction by 10%.
Chamco Digital has also contributed to this space. One of our clients, a manufacturing firm in Illinois, faced high defect rates in its production line, leading to costly recalls. Using our cloud solutions on Microsoft Azure, we implemented AI-driven quality assurance to detect defects in real time and integrated IoT sensors to monitor production metrics. We also used Power BI to provide dashboards for tracking quality performance. Within six months, the firm reduced defect rates by 20% and saved 10% on quality-related costs. This project demonstrates how Chamco Digital’s cloud solutions can deliver measurable results for quality assurance.
The Future of Quality Assurance in Manufacturing
The future of quality assurance in manufacturing is promising, with several trends shaping the landscape:
- AI-Driven Quality Control: AI will become more sophisticated, enabling more accurate defect detection and quality predictions, such as identifying potential issues before they occur.
- Augmented Reality (AR): AR will enhance quality assurance by providing workers with real-time guidance, such as overlaying inspection instructions on a product.
- Sustainability Focus: Quality assurance will support sustainability goals, such as reducing waste by minimizing defects and rework.
- Integration with Smart Factories: Quality assurance will integrate with smart factory initiatives, enabling real-time coordination between production and quality systems.
Chamco Digital is well-positioned to support these trends. Our expertise in cloud migration and Microsoft Azure integration ensures that manufacturers can implement the infrastructure needed for AI-driven quality control and smart factory integration. We’re also committed to supporting sustainability through efficient, waste-reducing solutions.
How Chamco Digital Can Help
At Chamco Digital, we’re committed to helping manufacturers achieve quality assurance. Our end-to-end cloud solutions, powered by Microsoft Azure, provide the foundation for high-quality production systems. Here’s how we can help:
- Cloud Migration and Quality Management: We deploy cloud-based quality management platforms, ensuring that manufacturers can monitor and improve quality in real time. Our cloud migration services ensure a seamless transition to the cloud.
- AI-Driven Quality Assurance: We leverage Microsoft Azure’s AI capabilities to detect defects and ensure quality, reducing errors and improving product standards.
- IoT and Computer Vision Integration: We integrate IoT and computer vision with Azure, enabling real-time monitoring and automated inspection of production processes.
- Managed IT Services: Our managed IT services include continuous monitoring, updates, and support, ensuring that quality assurance systems remain reliable and effective.
By partnering with Chamco Digital, manufacturers can reduce defects, ensure compliance, and enhance customer satisfaction. Our proven track record, as demonstrated by our work with the Illinois manufacturing firm, shows that we can deliver results that drive success.
Conclusion
Quality assurance is essential for manufacturers looking to reduce defects, ensure compliance, and enhance customer satisfaction. By leveraging technologies like AI, IoT, and cloud computing, manufacturers can monitor and improve production processes, ensuring that products meet the highest standards. However, achieving these goals requires overcoming challenges like data quality, cost, and integration complexity.
At Chamco Digital, we’re committed to helping manufacturers navigate this complex landscape. Through our partnership with Microsoft Azure, we provide the scalable, secure infrastructure needed to implement quality assurance solutions. Our expertise in cloud migration, AI, and managed IT services ensures that manufacturers can build quality systems that deliver value and drive success. As the manufacturing industry continues to evolve, Chamco Digital remains at the forefront, empowering our clients to build a future where quality assurance ensures excellence and customer satisfaction.